Blog
DDMRP
Inventory Management, or the Toothache of SCM
A story of Hope, Fear and Solutions - Stemmer Company
If you ever find yourself heading to the dentist—a necessary but often less-than-enjoyable experience, particularly in Western Europe—you'll likely encounter supplies and auxiliary materials distributed by Stemmer.
Stemmer, a family-owned company with over 40 years of experience, serves more than 90,000 customers, primarily dental offices. Managing an extensive inventory of over 70,000 SKUs and collaborating with approximately 600 suppliers, Stemmer operates three warehouses, one of which is the largest in France, collectively facilitating approximately 1,300,000 deliveries annually. This equates to an impressive average of over 1,700 operations per day per warehouse.
Given Stemmer's commitment to customer satisfaction, they distinguish themselves by offering complete sets in a single delivery upon order placement. However, managing such complex logistics requires meticulous planning to ensure the availability of products from various suppliers in the expected quantities and timelines.
Despite their efforts, Stemmer has encountered operational challenges, often resorting to maintaining excessive inventory or relying on expedited deliveries during stockouts, both of which result in additional costs. Consequently, achieving set targets has remained a persistent challenge for the company.
Interestingly, Stemmer implemented an ERP system in 2016 with the aim of standardizing distribution management. However, it appears that they may have overlooked an article by our colleague Konrad Grondka regarding the implementation of such systems. Instead of adhering to best practices, external programs for process management began to emerge, leading to a surge in the use of Excel spreadsheets. Consequently, despite the substantial investment in ERP, planners opted for the significantly cheaper and seemingly more efficient spreadsheets, citing that "it worked better." As a result, issues continued to compound over the years.
To address the problem effectively, it is essential to first understand and analyze it comprehensively before selecting appropriate methods and solutions. Stemmer has identified three main issues:
- Low product availability, which has detrimental effects on both the company and its customers. Inadequate availability not only hampers the company's ability to fulfill orders but also impacts the customer experience negatively. For instance, delays in treatment can occur, with even every fifth tooth left untreated on time, significantly affecting patients' well-being.
- Class A - ~ 85%
- Class B - ~ 88%
- Class C - ~ 80%
- Uncontrolled inventory growth
- Pressure to increase employment in the planning department due to the standard 8-hour workday for planners proving insufficient to manage the growing chaos, particularly exacerbated by the challenges of operating in a pandemic environment.
After an extensive decision-making process, the company opted to implement DDMRP. Initially, a pilot program was launched in one location, encompassing all of the over 10,000 SKUs currently in demand. At this location, a team of 8 planners managed relationships with 19 suppliers.
Following several months of the pilot phase, notable results emerged, particularly regarding material availability:
- Class A product availability - increased from ~85% to >98%!!!
- Class B product availability - increased from ~88% to >95%
- Class C product availability - increased from ~80% to >90%
- Additionally, the implementation of DDMRP led to improvements in data quality, resulting in enhanced management capabilities at all levels.
With such remarkable results, in mid-2021, the decision was made to fully implement DDMRP in France, encompassing over 45,000 SKUs and involving more than 600 suppliers. Several key areas emerged as focal points, all hinging on the availability of high-quality data:
- Ensuring not only the availability of individual materials but also complete sets for dental offices. Customers expect the convenience of assembling and receiving orders from a single source, emphasizing the importance of timely and complete deliveries.
- Strengthening collaboration and data/forecast sharing with suppliers to ensure adherence to new regulations while optimizing availability. Given the absence of in-house production, effective collaboration is essential for operational efficiency.
- Conducting analytical work with planning and making adjustments in response to a dynamic environment. Centralizing data sources for decision-making and eradicating reliance on "tribal knowledge" are imperative for informed decision-making.
- Fostering cooperation within the organization through the utilization of DDMRP tools and methodologies. Emphasis is placed on communication, team building, and the dissemination of best practices to optimize internal processes.
In December 2021, a comprehensive summary was conducted. Despite the challenges posed by the pandemic and the complexities of supply chains during this period, remarkable availability levels exceeding 98% were achieved for each of the ABC classes.
The most prominent benefit highlighted was the newfound capacity to focus on daily challenges. Previously, planners dedicated over 5 hours per day to planning duties alone. However, post-implementation of DDMRP, this time commitment has been significantly reduced to approximately 0.5 hours per day.
This surplus of time presents opportunities for leveraging DDMRP functionalities to address various challenges, including:
- Optimization of transportation, particularly considering that customers often expect transportation to be included in the price.
- Maximizing the utilization of truck/container capacity (FTL/FCL).
- Ensuring simultaneous availability of goods from multiple suppliers for a single order.
Furthermore, for servicing 45,000 SKUs and managing relationships with 19 suppliers in France, only 5 people are now required, compared to the previous requirement of 8 planners, to oversee information and material flow.
Following implementation in France, financial reports indicate a notable reduction in inventory by over 12%. The organization is now gearing up for DDMRP implementation across its entire operation in 2022.
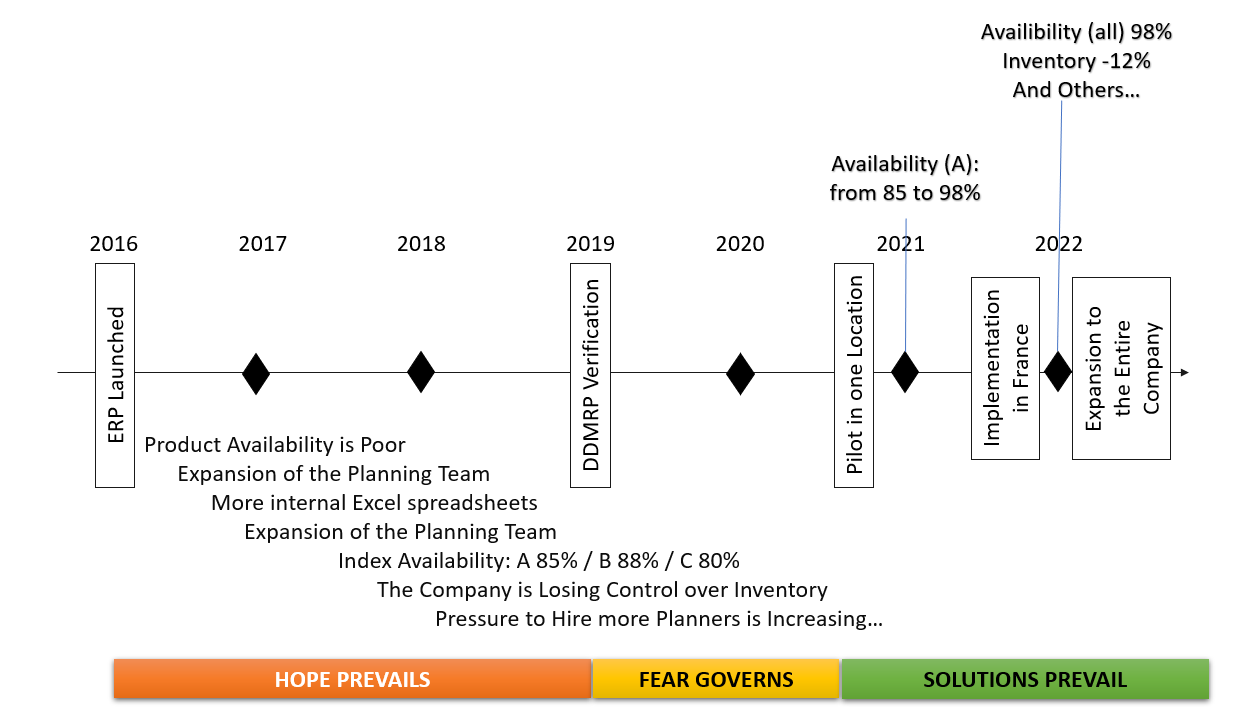
In summary:
- Decreased inventory costs: Achieving a reduction in inventory by over 12%.
- Improved inventory structure and elevated levels of customer service: Achieving availability rates of 98% for all categories, marking an increase of 10 to 18 percentage points.
- These remarkable outcomes were realized by nearly 40% reduction in the planning team while simultaneously slashing operational workload by over 90%!
Additional benefits include:
- Reduced delivery costs through enhanced utilization of truck and container capacity.
- Stabilized delivery schedules and enhanced collaboration with suppliers, leading to minimized costs associated with expedited shipments and additional transports.
- Optimal utilization of warehouse space without the necessity for emergency expansion.
It's understandable to be apprehensive about embracing new solutions; after all, it entails embarking on another major project accompanied by additional expenses, with no guarantee of success. But what if we could significantly mitigate this risk?
Are you interested in exploring a risk-free implementation plan? Click the button below to visit the page where you can download the DDMRP implementation plan
author: Aleksander Okraska